This article was originally written by Chris Rugowski and published on Sept. 23, 2024 in The Business News.
OSHKOSH – Students in Fox Valley Technical College’s (FVTC) Woodworking Technology program were greeted by a new piece of equipment when they entered the woodworking lab this semester.
FVTC acquired a new Altendorf sliding table panel saw that uses AI to increase safety for operators, increase accuracy in cuts and help increase production time.
Instructor Glenn Koerner said not only does the sliding table saw have state-of-the-art features to process wooden components with high-level precision, but it also comes with a hand safety assistance system, a feature powered by AI.
New tech for a tech-savvy age
Koerner said he and fellow instructor Mark Lorge went to the International Woodworking Fair in 2022 looking for the cutting edge in technology, so they can make sure to put it in front of their students in the coming years.
“We had seen (the HAND GUARD hand safety system) at that show and thought it would be great to have that tech in front of our students,” Koerner said. “We wanted to get the experience and exposure to new technology, and also for the safety aspect. It’s great to have students who have never used equipment like this before have peace of mind knowing they won’t hurt themselves.”
Developed by Altendorf Group – a wood-processing machinery maker based in Germany – Koerner said the HAND GUARD hand safety system collects more than half a million pictures and references from real hands, tattooed hands, hands with amputated fingers, hands with different pigmentation, etc.
He said it then uses AI to form a virtual “super hand.”
When a saw operator’s hand is captured by one of two cameras projecting down on the tabletop, Koerner said the hand is matched against the AI-created “super hand” and the system reacts accordingly.
Somewhat similar to a traffic light display, the saw uses green for ready, orange as a warning and red when the machine stops.
“When students begin, the overhead cameras identify the operator’s hands, and the visual display on the blade guard will start with a green light,” Koerner said. “Anytime while in operation, if a hand starts approaching dangerous proximity to the blade, the blade guard will change colors. If a hand moves rapidly toward the blade or gets too close, the display turns from orange to red and within a split second the blade drops and the system shuts down.”
Koerner said resetting the system is simple, too, pushing a button and 30 seconds later the blade resets to its exact position as it was and the operator is ready to get back to their work. Another nice aspect of this, he said, is that nothing gets damaged or destroyed from the blade to the wood being cut.
Though the safety feature is a tremendous asset in the learning lab, Lorge said students will still be taught about safety and not rely solely on technology to tell them when they’re in trouble.
“We do enough with our instruction to make sure students know this feature might not be something they have in the workplace,” he said. “Students still have to learn how to operate equipment safely but when you have someone coming in with no experience, this is a great protection for them until they get that experience.”
Catching on
As tech becomes more and more prevalent across industries, Koerner said he feels fortunate to be able to have HAND GUARD in the classroom for students to use.
He said there are only three other HAND GUARD saws like this in Wisconsin that he is aware of.
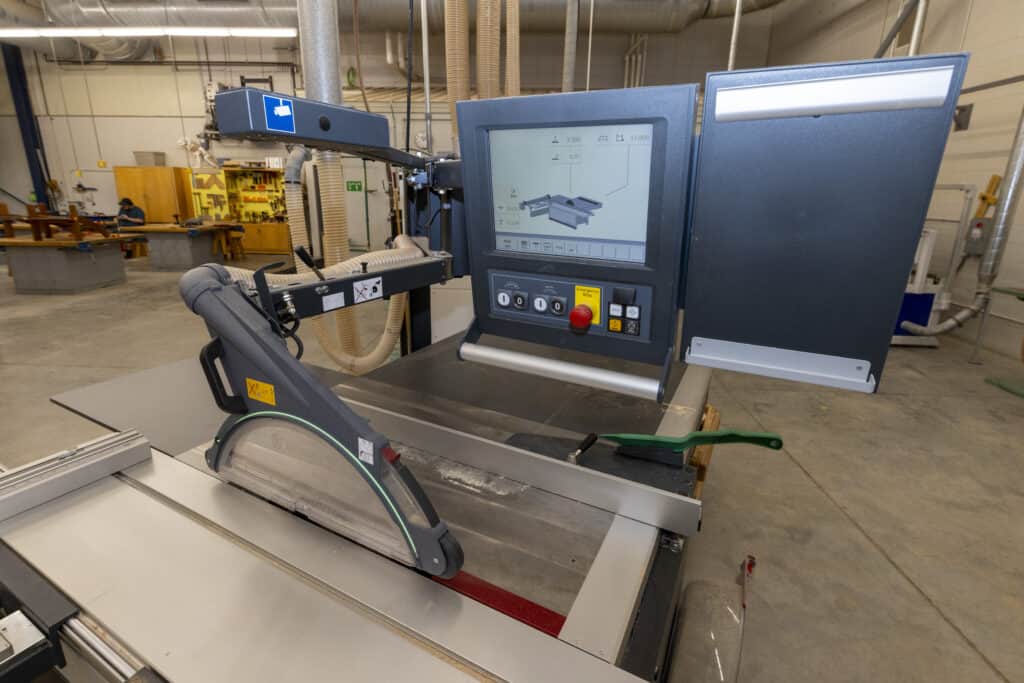
“It’s very operator-friendly, very efficient and extremely accurate,” he said. “So, you ultimately save production time with it.”
Koerner said the college was excited to get one of these when they heard of the technology and how good it was, noting that the machine in a roundabout way is also a good insurance policy to prevent injuries.
Koerner and Lorge said the system was popular amongst trade show attendees, and anticipates it to become industry standard soon.
“I would predict it’s going to be on every machine, large and small,” he said. “Certainly, it’s expensive at this point (coming in at between $75,000-$100,000), but as it gets more popular the cost will come down and the savings compared to someone getting hurt will pay for itself over time.”
Educating safety by setting off the machine
Koerner said first-time users of the HAND GUARD hand safety system often have an overly heightened sense of safety.
Students, he said, don’t want to set the safety system off fearing they are somehow causing damage to the machine.
The trick, Koerner said, comes down to hand position – the user really has to be cognizant of their hand positions and almost exaggerate where their hands are so that you’re not anywhere near where you can set it off.
This is a good thing, he said, because he sees students at other machines that don’t have these same AI safety features naturally begin to become more cognizant of their hand positions, exaggerating to keep their hands out of the cut path.
“The new saw is an added benefit helping us in teaching safety,” he said. “It shows that knowing your hand position, where the blade is and understanding the tool you’re using is all relevant and needs to be kept top of mind. Accidents are avoidable.”
Koerner said though first-time operators are timid, they quickly begin to appreciate the tech.
Impressions of the saw
Koerner said first impressions of the saw have been mixed.
More often than not, he said, operators don’t realize their hands are as close to the blade as they are, and it can be frustrating when the machine stops and you have to reset.
Though Koerner has 35 years of experience with this type of saw, prior to the AI technology, he said the HAND GUARD hand safety system has had him rethink how he operates on all types of machines.
“You have to retrain your brain in a way,” he said. “Some might say it’s oversensitive, though it’s a good reminder that you really can’t be complacent about where your hands are.”
Koerner said woodworking classes start with foundational skills, such as basic table saw, band saw, jointer and planer use.
About midway through the year, he said, they begin doing more advanced work with building cabinets and that’s where the saw really comes into its place.
“We cut a lot of veneers with it,” he said. “We cross-cut a lot of solid wood. It becomes used in almost every project by the end of the class, so learning to use this kind of saw is imperative.”
Applying AI into the real world
Koerner said the employers he has talked to in the area and across the country are all saying the hardest part right now is finding people who have the woodworking skills they need.
He said he thinks leveraging AI will help train people faster and make things easier.
“Automation is huge right now,” he said. “It’s getting harder and harder to find people… I think that the integration of AI, and automation will help bring more people into this industry, simply due to ease of use and safety.”
All in all, Koerner said he sees this type of technology being the norm in the industry in the coming years, sooner rather than later, and is excited to see and train the coming generations as he continues to be an advocate for the woodworking industry and being a leader to the implementation of tech like this.
National Association of the Remodeling Industry
The North East Wisconsin Chapter of the National Association of the Remodeling Industry is the homeowner’s resource for finding quality contractors, design-build firms, suppliers and other related professionals in northeast Wisconsin.
INDUSTRIES
CONTACT US
920-832-9003
NEW NARI
c/o The Startup Hub
2701 Larsen Road, Suite BA229
Green Bay, WI 54303
Website designed & maintained by Rogue Wave Marketing